External Enclosure Design
- Kevin Matthew Mukalel
- Feb 14, 2022
- 2 min read
The most common material used for enclosures is plastic because it is durable, lightweight and resistant to water. For prototyping purposes, general purpose PBT (Polybutylene terephthalate) was chosen as the material for the final design for its high strength, stiffness, and impact resistance [9]. However, one thing to note is that PBT will warp easily under high heat and is not ideal for thin-walled designs, so additional testing will be required.
Version 1 of the enclosure was designed to curve around the back of the helmet and is attached using 3M adhesive to meet the constraints for functionality and aesthetics and is seen below.

Update:
The design of the external enclosure required multiple iterations and is currently still being updated as the final PCB is to be designed.
Due to material and time constraints, the external enclosure test designs are to be 3D printed using ABS in a FDM printer. This allows for rapid prototyping of minor changes in the design. The final enclosure will be 3D printed using the PBT material, as the design will no longer be thin-walled as it will have a minimum thickness of 5mm for each wall for structural stability.
The main issues with the version 1 design are that there is no way to open and close the enclosure without destroying it, and the curvature makes it impractical to store the battery and PCB without becoming impractically large and impeding user comfort.
Version 2 solves these problems by using a typical snap fit electrical component box design that can easily fit all required components without issue. This design also includes a lip/groove feature that allows for a better fit between the top and bottom of the enclosure. The tradeoff made with this design is aesthetics as the box will no longer be flush around the back of the helmet but will instead require a curved mounting bracket that will attach it to the helmet.
Currently all newly designed parts are being 3D printed for testing and the only foreseeable changes would include a groove in the housing to allow for easy opening and rails on the bracket to help support the weight of the enclosure with components inside. The new design and the curved bracket are shown below:

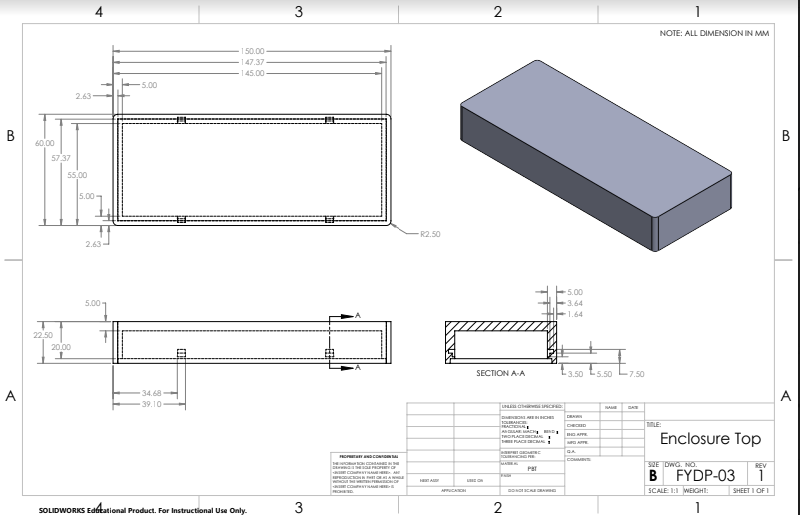
Comments